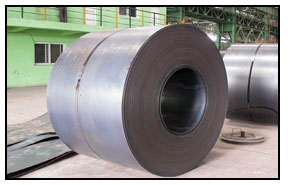
The recent
Trafotech 2012 exhibition and
workshop organized by
IEEMA brought to
light some weak spots in India's
transformer industry. In the context of the
country's power sector ambitions,
transformers are bound to play a decisive
role and addressing the industry's
concerns becomes imperative. This
special story by
Venugopal Pillai and
Mrinalini Prasad attempts to discuss the
most important challenges ahead of the
Indian transformer industry.
The transformer industry holds special significance
given that India is in the midst of a massive
upgrade of its power transmission & distribution
sector. It is only through an efficient network of
transformers can electricity travel from the power
generation plant to the final consumption centre. Again, it is
only an efficient and reliable transformer that finally helps a
power generation asset realize its socio-economic objectives.
Though India's transformer industry has matured over the
years, there are several concerns. Worse, some are only getting
graver with the passage of time. On the one hand, India's has
proved its technical prowess by producing 1,200kV
transformers—the highest voltage in the world, and on the
other, is still grappling with an embarrassingly high rate of
transformer failure.
This story special discusses three major challenges affecting
the transformer industry—the key raw material CRGO;
entry of China in the Indian market; and the country's
transformer management and testing abilities.
A. CRGO: THE KEY INPUT
The transformer industry's biggest concern continues to be
cold rolled grain-oriented (CRGO) steel. Whether it is absence
of domestic manufacturing, or imports of inferior material, the CRGO muddle eludes a lasting solution. In his keynote
address during Trafotech 2012, Ramesh D. Chandak,
President, IEEMA, noted: "The Second Steel Quality Control
Order, coming into effect from September 12, 2012,
mandating compulsory BIS-certification for CRGO electrical
steel will directly impact transformer manufacturers. This is a
serious situation and it will bring the entire Indian
transformer industry to a standstill in the very near future, if
enough number of mills is not certified by that date."
This observation is indeed pertinent and can be better
appreciated in light of some background. CRGO steel is a very
crucial input for manufacture of transformers and is
estimated to account for over half of the manufacturing cost
of a transformer. India, despite repeated attempts, has failed
to set up local manufacturing capacity for CRGO. As such, the
country's entire demand for CRGO—estimated at some 2.5
lakh tonnes annually—is met through imports. India has the
dubious distinction of producing the world's largest capacity
transformer of 1,200kV but is yet bereft of technology to
produce its most important feedstock.
CRGO is produced by only a few companies worldwide—
around 14 of them—and the technology is very closely
guarded. This is perhaps why technical collaborations with
Indian companies have not been forthcoming. The basic
contention with imported CRGO is about the quality of the
material. Alongside the prime quality CRGO entering the
country, there is also a significant volume of defective or
substandard CRGO that makes its way into Indian
transformers. It is this non-prime CRGO that has been the
biggest impediment.
In several interactions that Electrical Monitor has had with
transformer manufacturers, it was very evident that the scrap
CRGO problem in turn has two aspects. On the one hand,
there are marginal distribution transformer manufacturers
that intentionally use cheap and substandard CRGO, helping
them to quote lower during the procurement process of
power utilities. On the other hand, there are manufacturers
that end up using substandard CRGO out of ignorance.
Reason: there is simply no way to know the quality of
imported CRGO.
The ministry of steel attempted to correct this situation
through an order that mandated the use of only BIS-certified
electrical steel by India. The order comes into force on
September 12, 2012. The order was done in right spirit and it
also earned the acknowledgement of Indian transformer
manufacturers. On their part, trade associations like Indian
Transformer Manufacturers Association (ITMA) also offered
assistance to foreign CRGO manufacturers to get their
products BIS-certified.
It now turns out that out of the 14 global CRGO
manufacturers, only three have got their products BIScertified.
If more manufacturers do not get their products
duly certified, India stands to face multiplicity of problems;
lack of CRGO stock would be just one of them, noted R.D.
Chandak at the event.
It is interesting to note that the steel quality control order
has no implication on imported finished goods. As a result,
while Indian manufacturers would be struggling to get hold of
BIS-certified CRGO for their transformers, imported
transformers could unmindfully gain entry into the Indian
market. In keeping with the country's power sector
ambitions, transformer manufacturers over the years have
significantly enhanced their production capacity. In the
absence of certified CRGO, this capacity could turn
unproductive and the domestic demand could end up being
fulfilled by imports. This is a needless eventuality of the steel
quality control order, some industry players feel.
The steel quality control order is a step in the right
direction. However, its implementation and enforcement
might not be a smooth affair, industry players feel. Asis Das,
Managing Director, Stanelec Pvt Ltd, was of the opinion that
it would be impracticable to enforce "September 12" as the
deadline. In his view, only four global manufacturers have got
their products certified and it just cannot be the case that
these four satisfy the entire country's demand. Das felt that
an extension of the deadline would be the most obvious next
step. "An extension of six months could be a feasible option,"
he said. In all this, Das strongly recommended the
government diktat on BIS certification and said that it needs
to be implemented in the interest of all conscientious
transformer manufacturers.
Untitled Document
PGCIL, RINL to make electrical steel |
Rasthriya Ispat Nigam, better known as Visakhapatnam Steel
Plant, has signed an agreement with Power Grid Corporation
of India for setting up a joint venture route to make electrical
steel. The new project envisages setting up of a hot strip mill to
produce CRGO and CRNO steel. The total investment in the
venture would be around Rs.3,000 crore. The new facility will
annually produce 1.5 lakh tonnes of CRGO and 1 lakh tonnes of
CRNO.
Incidentally, RINL and Power Grid are also involved in another
joint venture for the manufacture of transmission line towers
and tower components. The MoU to this effect was signed in
December 2011.
It may also be mentioned that Steel Authority of India was to
partner with BHEL, MOIL and Power Grid Corporation for a joint
venture to produce electrical steel. SAIL opted out of the venture
in March 2012, paving the way for RINL to join. SAIL, in the early
1990s, had also made an abortive attempt to produce electrical
steel at its Bokaro plant in Jharkhand. |
Echoing this view was Amit Saraf, Director, Saraf Electricals Pvt Ltd. He was very supportive of the order and noted, "There
is no moving back from here." He admitted that there will be
practical difficulties in implementing the order but "teething
problems always exist and can be addressed." Garg also noted
that there were some issues in the order that need
clarification. For instance, whether the BIS-certification
applies only to transformers manufactured in India or does it
even cover transformers imported. He also agreed with
IEEMA's view that if CRGO availability was hurt, people
could resort to importing transformers from China, mainly
taking advantage of the competitive pricing. Garg was
however hopeful that the government would work out an
interim solution given that honouring the September-12
deadline would be easier said than done.
While the overall perception that Electrical Monitor derived
from the interactions was in support of the quality control
order, it is also worth looking at the inherent shortcomings in
the government's noble intentions. By its nomenclature, the
government's intention is to bring about some quality control
on the electrical steel (CRGO) used. The only way that the
government could achieve this was to impose some standard
of quality, which has now taken the form of "BIS
certification."
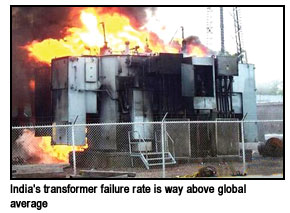
The moot point here is that not all imported CRGO is of
inferior quality. It is possible to use scrap CRGO to make
quality transformers. The practical difficulty is that there is
no way to readily know the quality of CRGO, and this is what
the government has attempted to address through the quality
control order. Recalling the genesis of imported CRGO, R.V.
Shah, CMD, High-Volt Electricals Pvt Ltd, noted that there
was a time in the 1980s when prime quality CRGO was in
short supply globally. This resulted in a sharp increase in
prices, making it economically unviable to make transformers
using prime grade CRGO. Indian manufacturers then started
designing transformers with scrap (used) CRGO. This is how
non-prime CRGO entered the Indian transformer milieu.
Shah also made an interesting observation that if a
transformer is designed to use "non-prime" CRGO, using
prime material may not be advisable. The nature of CRGO has
to be factored into the transformer design, he explained. "We
cannot condemn all forms of secondary CRGO as being substandard.
It is possible to make a good transformer using
secondary CRGO," Shah observed. He even mentioned that
the transformer design is as important as the quality of
material used. In a lighter vein, Shah noted, "One can always
make a bad transformer using the best of materials!"
All transformer manufacturers that Electrical Monitor
interacted with admitted that the quality control order has its
limitations, but something urgently needs to be done about
the intentional and willful use of secondary CRGO by a
growing tribe of marginal distribution transformers.
Scrap CRGO, L1 and Failure Rate: India has the dubious
distinction of having the highest transformer failure rate, a
metric that is shamefully higher than that of even lessdeveloped
countries. Several studies on the subject reveal that
India's transformer failure rate is in the region of 20-25 per
cent, with the global level being less than 5 per cent.
Substandard transformers are weakening the distribution
infrastructure, which already is woefully inadequate. India's
current power deficit is arising not only by insufficient power
generation capacity; electricity cannot uninterruptedly reach
downstream consumption centres due to regularly-failing
transformers. One reason why such substandard
transformers are employed in service is the government's
archaic L1 procurement process—a system that ensures that
contracts are awarded to those quoting the lowest price (L1).
There is no scope to incorporate any qualitative aspect in this
price-centric philosophy. Transformer manufacturers are
known to quote ridiculously low rates while bidding for
government-backed contracts. A manufacturer of quality
transformers simply cannot match these rates, resulting in
contracts going the way of L1 bidders. This results in
substandard transformers getting pressed into service. A
power utility official requesting anonymity admitted that the
L1 methodology is defective but no power utility would like to
willfully override it. Deviating from the L1 norm could attract
the adverse attention of agencies like Central Vigilance Commission, etc, the source said.
The main reason why transformers can be sold at such low
rates is the intentional use of inferior scrap CRGO. Once
again, it is this intentional use that the steel quality control is
trying to fight— or at least address.
LIMITATIONS OF THE STEEL
QUALITY ORDER
While the intention of the government is trying to curb the
use of inferior CRGO, it has limitations. Assuming that a
CRGO supplier is interested in getting his products BIScertified,
there is some effort involved at the ground level.
"Government paper work in India is never easy!" noted R.V.
Shah of High-Volt Electricals. Secondly, one cannot
unilaterally assume that all producers of CRGO would be
interested in supplying to India, and prior to that, be willing to
undergo the routine of BIS certification. CRGO
manufacturers located in Asia could show more inclination
but one could not be sure of European suppliers for instance.
"Despite a big market in India, you cannot expect every
supplier to be interested," was what Shah observed.
If one assumes theoretically that only BIS-certified
electrical steel can be used in India, and that only a fraction of
the suppliers get around to certifying their products, we will
come to a situation where supply is short of demand. This is
more so because India today is fully dependent on imported
CRGO. Efforts to produce the material domestically have
proved elusive for decades on end. The demand-supply
mismatch so caused will obviously lead to a price rise. Given
that there are only a few manufacturers of CRGO worldwide,
it is very likely that suppliers form a cartel and artificially
wield prices.
Transformer manufacturers that Electrical Monitor
interacted with unanimously admitted that there would
some short of "extension" or "interim relief" on the steel
quality control order. The order cannot be implemented and
enforced in totality from September 12 onwards. At the very
practical level, the government must also think about what
happens of the imported CRGO that is already in the country.
Asis Das of Stanelec estimated that the country has enough
imported CRGO scrap to last for at least two years. Amit Saraf
of Saraf Electricals felt that it would be practicable for the
government to ban import of non BIS-certified electrical steel
with effect from September 12, 2012, but allow the use of
existing imported CRGO for a period of time. "The quality
control order cannot be implemented overnight," noted Garg.
Fresh thinking: An interaction with Vishal Gakhar,
Director General, IEEMA, provided keen insights into the
CRGO muddle. He also corroborated views held by
transformer manufacturers on the subject. Gakhar felt that
the basic objective of the order, which is to improve the
quality of Indian transformers, has to be acknowledged.
However, there is still not enough clarity on whether CRGO
alone can be held responsible for the overall quality of the
transformer. "At the same time, we need to support the
government's decision of preventing the import of
substandard CRGO. That is why we, at IEEMA, have always
been welcoming the step," he explained.
All the same, there are practical hindrances in complying
with the order. As of now, the order implies that effective
September 12, 2012, India will not be allowed to import non
BIS-certified steel. With only three manufacturers getting BIS
certification so far, there is bound to be a demand-supply
mismatch that can lead to higher prices of CRGO. An industry
source indicated that the three manufacturers in question can
barely supply a fifth of India's CRGO requirement. "It was
definitely felt that the first step should have been to get
CRGO suppliers to get BIS registration and then pass the
order," the top IEEMA official noted.
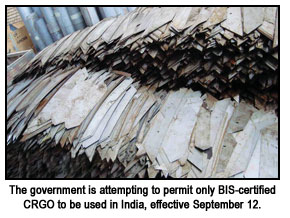
Regarding the process of BIS certification, Gakhar noted
that IEEMA was in dialogue with BIS to streamline the
registration process. There is need for a single window agency
that can help global suppliers to obtain BIS certification in a
time bound manner. He also observed that the quality control
order was coming at a time when the transformer industry
was going through a very harrowing phase. "The industry has
suffered a decline of over 7 per cent in the first quarter of FY13.
CRGO supplies have been disrupted over the past few months
and also with only three suppliers getting BIS certification so
far, the situation could turn even more challenging."
B. ROLE OF CHINA
While speaking of imports of electrical equipment, the very
term "China" evokes great interest. All through the XI Plan,
imports of power generation equipment from China was a
topic of much academic and policy debate. An estimated 40
per cent of the power generation capacity commissioned in
the XI Plan was based on equipment imported from China.
While the government did its bit to preempt Chinese
participation by imposing "local manufacturing facility" as a
prerequisite for tenders by government-owned power
utilities, China got its market share from private power
projects. India's focus is now on power T&D infrastructure,
and China is also moving in tandem.
The Indian transformer market has been identified as a
great business opportunity by Chinese manufacturers. India
has targeted to add 65,000 mw of new power generation
capacity in the XII Plan period. This translates to a demand of
1.95 lakh MVA, considering only power transformers-and not distribution transformers. China appears to be interested in
supplying large high-end power transformers where the
business margins are highest.
Considering all forms of transformers used in the power
sector, the total demand in the XII Plan period is estimated at
500,500 MVA. Besides, transformers worth 238,150 MVA
would need to be replaced, according to an IEEMA estimate.
Thus the total transformer market in the XII Plan period is
estimated at 1.48 lakh MVA per year.
According to estimates made by Electrical Monitor, domestic
production of transformers is likely to have reached 2.3 lakh
MVA in FY12, up from an estimated 1.91 lakh MVA in FY11
and 1.53 lakh MVA in FY10. Capacity utilization of the Indian
transformer industry, as reliable statistics suggest, is between
65 and 75 per cent. The average annual production of
transformers has been rising steadily from 47,000 MVA in the
IX Plan (1997-02) to 83,000 MVA in the X Plan (2002-07). The
bygone XI Plan has seen the highest ever average annual
production of around 1.7 lakh MVA.
Untitled Document
The Dark Side of CRGO |
If one looks at the economic activity of making distribution
transformers using inferior scrap CRGO, it is a very lucrative one.
Non-prime CRGO could cost up to 50 per cent lower than the prime
variety. Further, the cost of CRGO in the total cost of a distribution
transformer could be anything between 35 per cent and 50 per
cent. Power utilities are "ready buyers" for such transformers as
they are hopelessly bound by the L1 procurement mechanism.
Every power utility knows beforehand the life expectancy of a
distribution transformer procured under the L1 route. Very
unwittingly, the use of inferior CRGO has gained formalness. After
all, inferior CRGO is willfully used only because there is a market
for it. Over the years, the activity of importing scrap CRGO steel
and its deployment in distribution transformers has turned into a
huge business with high and widespread stakes. The use of
inferior CRGO refuses to wane for decades on end. This coincides
with the fact that India has been unable to produce electrical steel
for the past fifty years. Industry players, through their tacit
admissions, do not see these two developments as independent.
|
Power Grid Corporation of India, the Central transmission
utility, is expected to be a big buyer of power transformers in
the XII Plan period. PGCIL has outlined a capital expenditure
of Rs.1 lakh crore for the XII Plan period. An estimated 70 per
cent of this will be in procuring equipment while 30 per cent
will be towards contracts. An industry expert opined that
transformers account for one-fifth of PGCIL's total
equipment purchase. Hence, PGCIL alone is expected to
spend around Rs.15,000 crore on purchasing power
transformers in the ongoing Plan period.
According to very reliable information, PGCIL has already
begun purchasing from Chinese suppliers. However, it is not
clear as yet whether the CTU is insisting on transformer
suppliers to have a local manufacturing base. In the early
months of FY13, PGCIL is known to have procured power
transformers from Chinese suppliers like TBEA Shenyang
Transformer Group Co Ltd, Hyosung Corporation and
Baoding Tianwei Baobian Electric Co Ltd. Contracts have
been awarded on the international competitive bidding route
where Chinese suppliers have clinched deals in direct
competition with Indian, multinational companies and even
other Chinese contenders.
The new approach: Whilst catering to India's power
market, China is now seen to be adopting a new approach,
which is more sympathetic to India's ideologies. China
appears to be very serious in setting up a manufacturing base,
unlike in the past when it was a mere supplier without a local
manufacturing presence. The dissent over China was largely
due to the lack of "level playing field" between Indian and
Chinese equipment. This was mainly in the context of main
plant equipment for thermal power plants where Chinese involvement was at its peak.
Two big names in the Chinese transformer industry—
TBEA and Baoding Tianwei Baobian (known as TWBB)—are
on their way to set up their manufacturing base in India.
Incidentally, both of them have homed down their site
selection to Gujarat. TBEA has formed a 100 per cent
subsidiary TBEA India Pvt Ltd and is investing Rs.2,500 crore
to set up a greenfield facility for power transformers at Karjan
near Vadodara.
TWBB has selected Gujarat-based Atlanta Electricals Pvt
Ltd to form a 51:49 JV called BTW Atlanta Transformers India
Pvt Ltd. The manufacturing plant, also near Vadodara, is
likely to go into production in May next year. Power
transformers in the range from 220kV to 765kV will roll out
from the plant with the possibility of making 1,200kV
transformers in future.
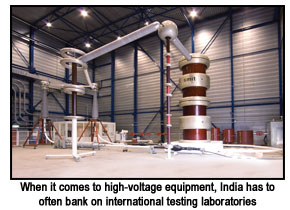
With China very serious in setting up a manufacturing base,
there should be no reason for Indian manufacturers to object.
China's involvement is now a legitimate expression of foreign
direct investment. Some transformer manufacturers that
Electrical Monitor got in touch with appeared rather
unfazed about Chinese competition. "Once they put a plant,
they become like Indian players. They will face the same
headwind that we (local players) face," noted Jaideep Jain,
Director, Tesla Transformers Ltd, in an earlier interaction with
Electrical Monitor.
C. TRANSFORMER MANAGEMENT & TESTING
Given that India's transformer base is set to expand
substantially in the coming years, transformer management
and testing will be crucial areas. Trafotech 2012 touched upon
this vital aspect. In his presentation at the event, Pierre Lorin,
Global Technology Manager - Transformers Service, ABB
Secheron Ltd explained that India's ageing assets, rising
energy demands and the need to deliver without unplanned
outages are few challenges faced by utilities and industries
alike. Lorin said, "The apparently contradictory demands of
more transformers but less investment can be met through
optimized asset management. But it requires accurate and
reliable models considering both technical and economic
criteria. Some of the key components of asset management
can be addressed through condition-based assessment, online
monitoring and economical analysis. Ultimately India will
have to spend money on the right asset at the right time."
On the subject of transformer testing, Electrical Monitor
interacted with a few event participants who generally agreed
that India needs to do much more in terms of testing of highvoltage
equipment like power transformers. "We need to
invest more in our testing facilities and we also need to
demonstrate our facilities at an international level," said
Ramesh Chandak, MD & CEO, KEC International who is also
President, IEEMA. Chandak also noted that the waiting
period at the testing institutions has to reduce. India's testing
system needs to be brought at a level where it would be
accepted by the world. Giving an example, Chandak noted
that China already has two testing institutions that are
accepted internationally.
R K Tiwari, General Manager - Transformer, Capacitor &
Bushing, BHEL Bhopal, noted "Our testing facilities with
most manufacturers and Central testing facilities are at par
with international standards." Tiwari cited some testing
laboratories of CPRI, Alstom, BHEL-Bhopal and ABB as being
of the international mark.
Suggesting that there is much scope for improvement was
Adityaa Dhoot, Joint Managing Director, IMP Powers Ltd.
"Testing labs on our country need immediate upgrade in terms
of voltage as well as capacity. The government has recently
allocated funds to CPRI and they are working towards it.
Testing has to go hand-in-hand with the capacity addition,"
was what he had to note.