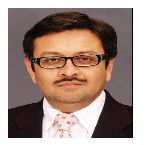
—
Deven Doshi, President, Association of Indian Forging Industry
AIFI has been the mouthpiece of the Indian forgings industry
for over four decades.
Deven Doshi, in an interaction with
Electrical Monitor, discusses the forging industry in depth
and explains how it is evolving and equipping itself to meet
ever growing demands from the industrial sector. Doshi also
explains how the industry is now weaning away from its
traditional thrust on the automotive sector and foraying into
newer areas like power equipment, oil & gas, aerospace, etc.
An interview by
Venugopal Pillai.
Tell us about the size of the Indian forging industry and the growth seen in recent years.
The forging industry has emerged as a major contributor to the Indian manufacturing
industry. The total size of the industry is estimated to be around

13,200 crore with over
25 per cent attributed to exports.
The Indian forging industry is highly fragmented, with around 400 units—out of
which only 9-10 are large units—scattered all over India. Briefly, the composition of the
Indian forging industry can be categorized into four sectors-large, medium, small and
tiny. SMEs form the backbone of the industry.
The organized sector accounts for about 65-70 per cent of the total forging production
in the country and mainly caters to the closed die-forging segment. Unorganized players
(mainly small and tiny units) cater largely to job work and the replacement market or
tier-3/tier-4 component manufacturers and predominantly focus upon the open-die
forging segment that is less capital-intensive.
A wide range of products are manufactured, each being a diverse market structure
and technology requirement. Over 60 per cent of the forgings produced are utilized by
the automotive sector. However, the industry's efforts in upgrading technologies and
diversifying product range have enabled it to expand its base of customers to power,
diesel engines, aviation, defense, agriculture, mining, oil and gas, industrial machinery,
shipping, space etc.
What is the current membership of AIFI and its geographical spread? How has AIFI
membership grown in recent years?
The AIFI family at present consists of about close to two hundred members, who
command a large market share of about 75 per cent of the total production of the Indian
forging industry.
A large segment is represented by western region comprising of Maharashtra and Gujarat followed by northern region, southern region etc.
Membership growth was affected during 2008-09 and part of
2009-10 due to the economic downturn, it has started looking up
since 2010. AIFI's membership grew by more than 10 per cent in
the last fiscal year.
What is the role of SME in the Indian forging industry and what is
the representation of the SME sector in AIFI?
As said earlier, the composition of the Indian forging industry can
be categorized into four sectors—large, medium, small and tiny.
As is the case world over, a major portion of this industry is made
up of small and medium enterprises (SMEs). Only about 5 per cent
is made up by the large enterprises in terms of number and around
30 per cent consists of small and medium sectors.
What are the key objectives of AIFI with respect to promoting
growth in the Indian forgings industry?
The key objectives and measures for promoting growth can be
summarized as follows:
- Production of forgings for the non-automotive sector is on the
rise leading to a more balanced customer portfolio. Identified
drivers of growth in the non-auto sector are aerospace, energy,
oil & gas and heavy engine parts.
- The Indian forging industry needs to leverage the market
opportunity through focused increase in productivity
rather than mere capacity expansion, technology
upgradation and modernization of the units to comply with
global quality standards.
- The small sector forging units need to improve their operational
efficiencies by allocating a certain percentage of their capital
investment to technology upgrade. This will help them to
maintain consistent surface quality requirements of the product
and meet strict pollution control norms. Testing and inspection
facilities can be outsourced for these units.
- The organized sector should continuously acquire latest
technologies with added emphasis on IT, CAD/CAM, and other
forms of computer-based technologies to produce quality
forgings conforming to international standards with best yields.
- Energy audits are being used as an important way to reduce
consumption of costly oil and power, as also to make industry
environment-friendly.
- Forging units should involve in reduction in plant inventory
through "just in time" procurement and ensure prompt delivery
commitment of the products for sustainable confidence of
automobile manufacturers.
- Inorganic growth is another strategy to expand the global
footprint and establish a global presence in some of the world's
largest markets.
- Also considering different geographies follow separate
business cycles, it is necessary to reduce one's overdependence
on a single market. This strategy can additionally
help the industry to take advantage of the varying differential
growth opportunities across different geographical regions and
also different parts of the globe.
What is your view on the competency level of the Indian forging
industry? Do you see India inclined to adopt foreign technology
through collaborations?
While the automotive industry is the main customer for forgings,
the industry's continuous efforts in upgrading technologies and
diversifying product range have enabled it to expand its base of
customers to emerging sectors including aerospace, energy, oil &
gas and heavy engine parts.
Also the Indian forging industry is increasingly addressing
opportunities arising out of the growing trend among global
automotive OEMs to outsource components from manufacturers in
low-cost countries. With the result, Indian forging industry has been
making significant contributions to country's growing exports.
Please summarize the status of the Indian forgings industry with
respect to application in the power sector.
The industry majors are keen to have a more balanced customer
portfolio considering its heavy dependence on the automotive
sector. They would like to leverage the market opportunity having
identified drivers of growth in the non-auto sectors such as
aerospace, energy, oil & gas etc. In the power sector captive
capacities are also being built. Bharat Forge, a major company in
the forgings industry, has floated a company to cater to the needs
of the power sector.
What is your view of the supply chain management standards of the
Indian forgings industry with respect to supplying to power plants?
The forging industry is used to working on tight schedules with the
automotive industry and as such should not find it difficult to
maintain schedules with power sector as well.
What is your overall outlook for the Indian forgings industry and its
prospects for the medium term?
The Indian forging industry has been growing at a compound
annual growth rate of 29 per cent from 2003 onwards, and on an
average exports contribute around 25 per cent of the industry's
production. FY2010 was a good year for the forging industry.
The revival which started in October 2009 picked up momentum
during last year. Overall production of forgings increased to about
1.8 million tonnes in 2009-10 from 1.05 million tonnes in 2008-09,
registering a strong growth of over 71 per cent.
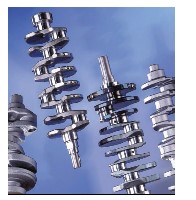
The production is expected to reach 2.3 million tonnes by March
2011. India exported forgings worth about $800 million in 2010-11.
This was a result of several industry initiatives including capacity
expansion, modernization, cost rationalization, coupled with a
revival in demand from the automotive sector and particularly the
passenger car segment which recorded an excellent growth.
The market potential continues to grow for the forging industry.
The growth of the automobile sector has provided a strong impetus
to the forging industry. The newer generation cars will require
better quality forgings. Looking at the overall long term picture, the
vehicle industry seems well poised to maintain a remarkable
growth rate of around 25 per cent.
This, obviously, will require the production of the Indian forging
industry to shift into higher gear and the industry is expected to
grow by about 25 per cent to reach

16,500 crore.